工业控制系统的发展经过三次历程:机械控制,电子控制,计算机控制。
随着工业互联网的快速发展,使得我们的生产数据可以进行规模化集中存储,实现以前不可能实现的大数据,并利用云计算平台前所未有的计算能力对这些大数据进行分析、挖掘和优化生产效率。工业4.0使得现场设备、机器和工厂已经变得“更智能”,所以我们可以谈论智能设备、智能机器和智能工厂。
但是,我们会发现,无论是工业互联网还是工业4.0,均未对工业控制系统的“大脑”PLC/DCS做出任何更进一步的技术变革。这种两头重中间轻的现象,就好比是高速路上的收费站,光高速路扩宽远远不能够实现更大的汽车吞吐,耸立在高速路上的各个收费站才是这条路上的瓶颈点,因此针对收费站现在都需要设置更多收费窗口,实现电子收费等举措改革而适应高速、快速增长的车流。适用于工业控制系统领域也是一样,控制的核心PLC设备不能够灵活扩展,这一限制无疑将会大大减弱工业控制系统灵活性和可扩展性。
随着工业智能化需求的日益增长,以传统PLC/
DCS为代表的第三代控制系统已经不能满足工业智能化的需求,目前业界针对工业互联网、工业4.0等的技术体系探索,重点将围绕PLC/DCS展开,从而实现第四代的控制技术。
第四代的控制技术一定是软件定义和虚拟化技术的结合,从而满足工业互联网及智能工业的控制需求。软件定义PLC/DCS通过答应用户更换或添加组件而不影响系统的其他部分,实现轻松的可扩展性和系统模块化。软件定义PLC设计为开放平台,答应用户选择优选组件和解决方案,这意味着用户可以灵活地选择不同的供给商(无供给商锁定)。
在工业3.0系统中,在同一个体系结构中使用多个供给商的组件并不那么简单,或者根本不可能。软件定义PLC中通常没有硬件依靠性,所以很简单迁移和重用软件。软件定义PLC使用虚拟化或软件定义技术,使用更多的软件而不是硬件,因为所需的硬件数量较少,所以降低了成本,缩小了占用空间。目标是提供现成的和可供销售的COTS(COTS=商业现成的)软件/硬件产品以实现整体解决方案的灵活选择和可扩展性。
虚拟化技术和软件定义的体系结构是以软件为中心的模式,在系统集中治理、网络处理和安全性方面具有优势。远程监控降低了运营成本,而维护工程师或操作员并不总是需要现场检查机器的状态;集中治理简化了远程监控,因为只需访问一个软件平台即可治理您的资产;通过云计算和使用智能传感器(包括通信能力和加载诊断的传感器),机器数据被推送到云端,数据可以通过用户界面(HMI)访问,机器数据可以用于猜测性维护,这意味着机器数据可以用来预估机器即将发生故障的时间。
软件定义架构的PLC更强调的是一种体系,一种实现思想。和软件定义网络、软件定义世界一样,PLC设备的智能化和标准化的体现就是典型的软件定义的PLC,包括PLC轻松连接至互联网:将APP和分析结果嵌入机器和云,实现智能化和自我意识;无需更换PLC硬件即可改变和升级PLC设备功能,为用户提供智能,实现持续改进;通过API和生态系统扩大工业互联网平台应用。
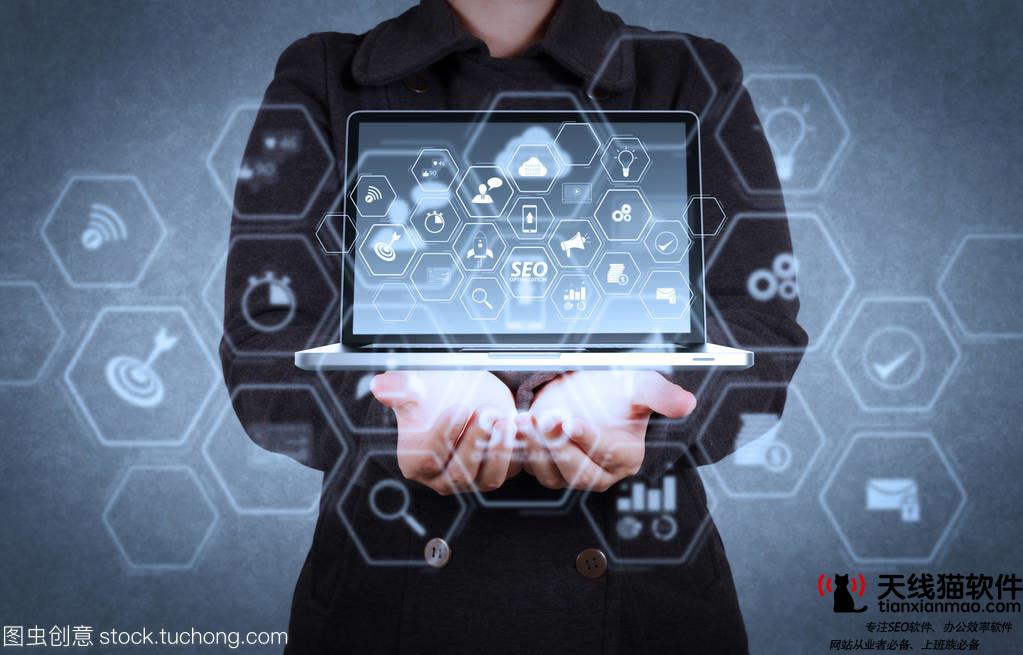
如果您觉得 工业互联网条件下新一代控制系统的发展趋势 这篇文章对您有用,请分享给您的好友,谢谢
文章地址:https://www.tianxianmao.com/article/online/5925.html
文章地址:https://www.tianxianmao.com/article/online/5925.html